Shawn Mills is a technology entrepreneur, founding member and president of Green House Data. You can find him on Twitter at @tshawnmills.
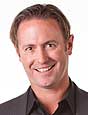
Greenhouse Data
This article series focuses on new data center facility development for small or medium operators, people who focus more on managed services and infrastructure development than building construction. Previous entries included planning for expansion, selecting a site, finding incentives, and deciding whether a realty and/or design partner is right for you.
Today, we will explore a bit more about designing an efficient facility, where design partners are the most useful and how site limitations and local ordinances force a compromise between the ideal infrastructure and realistic expectations.
Using Space Efficiently to Minimize Building Footprint
We covered some of the initial design process in our first post, namely deciding how large of a facility you need based on demand projections. A key factor for Green House Data was energy efficiency, a core aspect of our company value proposition and central to our business model. This also helped us determine facility design in many ways. When the design process reached a phase where we needed to settle on the building size, we worked backwards from our power goals.
For instance, we knew we wanted an average of around 5 – 5.7 kW of cooling per cabinet in a 4 MW facility, and 4,000 kilowatts divided by this cooling level is around 700-800 cabinets. We’re able to have a ratio of 7,500 sq ft of support space for every 15,000 sq ft of data center space, with a significantly higher cabinet density than comparably sized data centers, because we place our cooling equipment outside. Between CRAC units, air handlers and free cooling systems, the air conditioning equipment takes up a dramatic amount of traditional white space. By planning for the cooling systems to be installed outside, we were able to maximize the amount of cabinets on the floor and squeeze every useful space out of the 35,000 sq ft building footprint. Of course, the smaller you can afford to make your building, the lower the total capital expenditure.
Where a Design Partner Really Helps
Designers are extremely helpful in reaching energy efficiency and physical space goals. We knew what kind of PUE we wanted in our limited space, and how many cabinets we wanted to fit. They made it happen, and we sorted out many other details along the way, such as:
- What does the building look like?
- How does it lay out on the site?
- What are some of the electrical redundancy decisions to be made?
- What is the right level of overall redundancy?
The design process has three stages: schematic documents, design documents and construction documents. As of this posting, Green House Data is finalizing our schematic documents, which include a package with everything that needs to be built. This package is used for budgeting and the budget is used to create the design documents in turn. You really see the balance between the over-engineered, and a “right” engineered highly reliable data center design. Budget and maximized efficiency always play a factor in these decisions.
We have set an efficiency investment target of 5-7 year payback. Design engineers will attempt to meet your goals while maximizing reliability, however its important to stay heavily involved to ensure you are getting the payback you are looking for. Once you get your hands on the schematic documents, you might need to dial back some of the expenditure, and they change the engineering accordingly for the next round.
Moving from Design to Construction
The design documents are used to get a bid from contractors for the actual construction. The construction crew and engineers work together to create the construction documents. While the plans are finalized, you can get rolling on site approval and permitting with local and state jurisdictions.
Our experience is that you need to plan for a significant amount of time during this process. It just takes time. This was even with us working with a highly motivated to help move the process along efficiently city building department. The closer you work with the permitting agencies, the smoother it can go. More on zoning and construction permits in our next post – stay tuned.
Industry Perspectives is a content channel at Data Center Knowledge highlighting thought leadership in the data center arena. See our guidelines and submission process for information on participating. View previously published Industry Perspectives in our Knowledge Library.